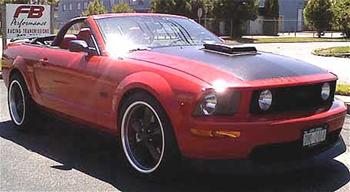
Introduction:
If you are reading this, chances are, you are considering swapping from the OEM Ford automatic to a FB Performance 4STB-E (4R70W/AODE) transmission on a 2005 (or newer) Mustang. Before you get all worked up, please understand that it does not take a neurosurgeon in order to accomplish the swap. You (or your mechanic) has to absolutely have the ability to perform normal drive-train work. More importantly, the ability to do neat and clean soldering is a must, (unless you plan on replacing a substantial portion of the wiring harness). If you do, then all you will need is the parts list (that follows).
If you decide not to replace the wiring harness, you are asking for trouble if you do not have basic soldering skills. If you do, you'll be amazed at how smoothly the changeover will go. This write-up does not go into detail about how to perform the actual drive-train work (See transmission Installation Instructions). It will, however, provide you with all of the details that are important for the swap.
There are (6) basic steps to accomplish this changeover:
1) Acquire necessary parts
2) Remove automatic transmission and related parts
3) Install the 4STB-E transmission, torque converter and related parts
4) Make several electrical connections
5) Replace Powertrain Control Module (PCM)
6) Have a Ford service tech set up your new PCM
Note: When converting from the Ford 5-speed Stick transmission the only requirements involve the replacement of the drive-line components. There is no concern regarding the PCM because the 4STB-E transmission has a full-manual valvebody and will utilize the same PCM that came with the Stick.
Things Worth Noting
A) You will reuse your existing cross-member with a supplied trans-mount bracket.
B) You have the option of replacing the driveshaft with a one-piece unit, but the driveshaft yoke must be changed.
C) You can retain the existing 164 tooth flexplate, but the torque converter adapter plate will have to be removed. The replacement converter will bolt directly to the existing flexplate. You also have the option of replacing the OEM flexplate with a heavy duty SFI rated version.
D) You will only use the supplied engine to trans. mounting bolts. (but do hold onto the original bolts)
E) Cars with the OEM Manual trans. have a relay (aux. relay #1) that is located under the dash on the driver's side. Automatic cars do not have it. The relay keeps the PCM hot for 1 second after the engine is shut down. We were not able to find out why the relay is there at the time of this writing, but is has not been of any concern so far because to date it has not been used in any conversion. The cars run fine with no warning lights on the dash. The only thing that was noticed when reading the trouble codes with a hand-tuner, was that it showed a code saying " low voltage to aux. relay". This might explain the only side effect which is a very slight delay before the starter responds to the key switch command.
F) As of this writing, the (2) harness plugs under the car for the reverse lamp switch and the output shaft speed sensor were also not available from Ford yet. Our instructions will show you how to make reliable connections here.
G) You will be running a custom wiring circuit (fused) in order for the reverse lamps to work. This is because your automatic wiring harness lacks the 2 pins in the PCM plug that completes this circuit.
H) You can probably avoid most of the electrical issues by replacing a substantial portion of the vehicles wiring harness. Many people choose not to do that. In our opinion, the process as described is a neat, clean and acceptable solution. I will satisfy the most demanding car enthusiast.
I) Read all of the instructions very carefully. Perform all work at your own risk. You an only you are responsible for decisions made and work performed. When this is done as described, it will result in a successful conversion. You also have the option of having a qualified shop do this conversion for you.
'05 & Up Mustang OEM Automatic to 4STB-E Transmission
Swap Parts List
(Qty) (Part#) (Description)
(1) SS16105-S-00 FB 4STB-E Transmission w/Various Options
http://www.fbperformance.com/viewtrans.asp?TransmissionID=76
(1) ---------------- 9" or 10" Full Race Torque Converter w/Single disk L/U (Multi-disk optional)
(1) F6ZZ*7007*EA Spacer plate (between engine and trans.- Optional)
(1) ---------------- Aftermarket SFI approved HD. Flexplate Optional
(1) ---------------- Polyurethane trans mount (AODE/4R70W type)
(1) 2-3-14061 1330 Heavy Duty Spicer Yoke (Lg. OD)
(1) ---------------- Trans mount/cross-member Bracket
(1) ---------------- Single piece Steel or Alum. Driveshaft (Optional)
(1) (Various) Aftermarket 3-speed shifter (w/FWD Shift pattern)
(1) 4R3Z*7277*ABD Gaiter (leather shift boot for use with Aftermarket Shifter)
(1) -MF (4STB-E opt) FB Multi-function Auto-reset Relay Controller for Overdrive & Lock-Up
(1) 5R3Z*12A650*ACD Reman. Manual trans. PCM (or have existing PCM re-programmed)
(1) --------------- 12-foot length of Corregated plastic harness tubing (5/16" or 3/8")
(1) --------------- 2-foot length of Heat shrink tubing for 16-18 ga. wire
(5) --------------- Top 5 trans. to engine mounting bolts have to be shorter than the ones that came
with the automatic. The new bolts should be 2 1/2"long excluding bolt heads
(1) -------------- Tube of 5-minute epoxy (General purpose, Get it at the auto parts store)
(1) -------------- Roll of Electrical tape
(20) -------------- Medium size Wire ties (tie wraps)
(1) -------------- In-line fuse holder with ten amp fuse
(1) -------------- Roll of 18 ga. wire
(1) 3U2Z*14S411*VBA Wire assy (pigtail)
(1) 3U2Z*14S411*SFA Wire assy(pigtail)
Special Notes:
J) It was recently brought to our attention that you do not have to buy a manual trans PCM (computer). You will however have to contact a highly qualified Ford technician or a tuning professional who can use Ford software to re-program your existing automatic PCM to eliminate all automatic functions. This will work on both the '05-'06 Mustangs. However with the 07 it will not, and no one has figured that one out as of this writing...you'll need a Stick PCM.
K) If you buy the 2 pigtails, the output shaft speed sensor and rev. light switch modification will not have to be performed. If you don't buy the pigtails you will see later in these instructions how to modify existing sensor and switch, but its recommended you buy the pigtails now that they are available.
Section A
R&R Drive Line Components
Lower the windows 1/4" because the battery will be disconnected. Remove h-pipe, and the following drive-train components: driveshaft, automatic transmission, converter and converter mounting plate. The original flexplate can be retained, unless an aftermarket piece is desired. The original shifter can also be reused if it is modified for the neutral lockout function. An aftermarket shifter with a 3-speed forward shift pattern can also be used. Some are equipped with a momentary push-button that is generally used for the optional trans-brake feature. The aftermarket shifter can be installed with the rubber boot, and leather gaiter boot.
Make a note as to the location of all (4) Oxygen sensors. You cannot mix their locations up. Each sensor must be installed in the same location on the exhaust system where they came from. Retain the original transmission fluid cooler and cooling lines, unless it is desirable to them with the #6 stainless steel braided type. Keep reverse light switch and output shaft speed sensor out of the transmission for now.
Install the 4STB-E transmission, and torque converter making sure that there is adequate converter-to-flexplate clearance (1/8 to 3/16 use drill bit as a feeler gauge). The OEM cross-member can be reused in its original location if the new cross-member bracket is used. If not, the position of the cross-member will have to be adjusted to the correct trans mount location. Install transmission mount. Confirm the distance from the back of the tail housing to the centerline of the rear pinion yoke to confirm the proper drive shaft length. Have the new yoke added to the existing driveshaft or to its replacement. The driveshaft, the h-pipe and anything else that was removed can now be reinstalled.
Section B
Install and Connect Wires for OD and Lock-up Auto Reset Controller
The Auto Reset Controller includes the following components:
(2) Momentary Push-button switches for Overdrive and Converter Lock-up
(1) Multi-Relay Pack with color coded wires
(1) Pressure Sensor switch (pre-installed on transmission)
Mount each of the Momentary switches in a convenient location either on the dashboard or the console. Secure the Relay Pack in convenient location that is not exposed to any heat (such as under in the console). This centralized location will reduce the amount wiring required. Use the following color-coded Wiring diagram to connect all of the various functions.
(Insert color-coded wiring schematic)
Section C
Oxygen Sensors and Output Speed Sensor Wiring Harness
You will now begin running the wiring harness to the proper locations and begin making circuit connections. You can refer to page 2 to see the differences between the auto and manual transmissions. When I did the swap, I used long tube headers and a new catted h-pipe which moved all four 02 sensors further back on the exhaust system. I had to extend the sensor harness sections in order to reach the 02 sensors. We chose to run the harness down the passenger side of the transmission with 2 harness extensions that went over the top of the transmission to the rev. lamp switch and the output shaft speed sensor. If you are using the stock exhaust, I suggest you run the harness down the driver's side of the trans like in the picture on page 2.
If for some reason you have a problem with wiring reaching one of the components, just extend that section of the harness using wire, solder, heat shrink tubing and the corrugated harness tubing. Just button up any extensions you make by making them look like the sections of harness that Ford has all over the car. Start with the front 02 sensors and work your way back. In other words, lay out the harness to see if your way is going to allow all of the connections to be made without too much soldering and extending harness sections. Once you have decided on which way to run the harness, start from front to rear (front 02 sensors first) and work your way back to the rear most connections. Remember, each 02 sensor must be connected to it's original position, you can't mix right and left sides or front and rear. The only circuits that are in play here are the four 02 sensor harness sections and the output shaft speed sensor harness section. Do not tape up the plugs that won't be used anymore. You will have a slight modification to do on one of them later.
For the output shaft speed sensor, just run the section of harness that goes to the output shaft speed sensor for now. Later, you will run a new 2-wire section of harness from the rev. light switch at the transmission up to the engine compartment.
Once you have the four 02 sensors connected and the one harness section that goes to the trans in it's general position, just leave the harness hang there without any wire ties to secure it to anything.
Section D
Wiring Reverse Lights - Speed Sensor Transmission Harness
The reverse light switch and output shaft speed sensor each have 2 wires that have to be soldered to them. If you look into their plug sockets, you will notice that the connector pins are too far inside of the sockets to actually solder wires to them. What you will have to do is cut the plug sockets down lower so the pins are much closer to the top opening of each socket. You want the connector pins to be just below the top of the socket opening. See page 5, pictures A and B. Don't laugh too hard my drawing. You can cut the sockets down with a dremel tool, hacksaw, cut-off tool or whatever you have that will make a decent cut. The rev. light switch will need two 18 ga. wires soldered to the connector pins inside of the switch. The wires should be 6 to 8 feet long because they will be run up to the engine compartment while being protected by some of the corrugated harness tubing. See page 5 picture B for solder connection view. After the wires are soldered to the pins in the switch, put the switch in a vice and fill the socket cavity with 5-minute epoxy or high temp. silicone. This will protect and seal the connections. Go under the car and pull the harness backdown off of the transmission. Take the section of harness that has the output shaft speed sensor plug on it and cut the plug off. it is the plug that is at the rearmost end of the harness. The two wires are dark blue with a yellow stripe and gray with a red stripe. Solder the wires to the pins inside of the cavityof the output shaft speed sensor. Then fill the cavity with epoxy or high temp. silicone.
Before you button up the transmission harness, look at the picture on page 2 of the automatic transmission. At the bottom of the picture you will see a harness plug labeled C167. Pin 10 and 12 of that connector have to be connected so your starter will work. See page 5 and look at the close up view of plug C167 so you can tell which wires are 10 and 12. The picture shows the opening of the plug. Cut the 2 wires from the back of the plug (not shown in picture). Solder the wires together and seal with heat shrink tubing. After that, install the harness back to it's final position with the rev. light switch and output shaft speed sensor installed on the transmission. Make sure you have the two long wires that come off of the rev. light switch protected with the corregated plastic harness tubing. All of the unused plugs that were for the automatic transmission should be completely sealed up with plenty of electrical tape and secured with wire ties. Secure the harness neatly to the transmission with wire ties and run the new reverse light switch harness up to the engine compartment and leave it near the fuse box for now.
Section E
Transmission Harness
Ok, so now you have 2 new harness sections that end up at the fuse box area. One comes from the transmission and the other comes from the strut tower. The one from the transmission has 2 wires in it. Solder one of the 2 wires directly to the single wire that comes from the strut tower harness. Seal the connection with heat shrink tubing. Now you have one wire left that is from the trans. harness. This wire has to be connected to a (+) power source. Before you do that, install an in-line fuse holder to the end of the wire, so that the new end has a fuse before the connection is made to (+). Install a 10 amp fuse in the fuse holder. You must have a fuse.
If for some reason the wiring harness ever shorts to ground, this will prevent a potential fire. I connected the fused wire directly to the (+) cable at the fuse box. The only problem with this is when I park the car and shut off the engine, the rev. lights will stay on if I leave the car in reverse. I never park in reverse, so that's ok with me, I park in 1st gear. If you want, you can probe the fuse box for a location that is only hot when the key switch is on, but I chose not to do that because I didn't want to pull extra amps from any circuit that is already in use. My biggest fear was the car's pcm possibly detecting the increased amp load and causing a problem. I doubt it would cause a problem, but this super smart pcm is beyond my comprehension, so why take the chance.
Section F
PCM Powertrain Control Module
Now, you can start the car. It will be in failsafe mode and will not run very well because the pcm thinks the transmission is overheated. There's probably a dozen or so signals that are no longer sending feedback to the pcm from the auto. transmission. This causes the pcm to protect the engine by limiting power. You will see a wrench light on the dash when you drive and the overdrive light will flash. The engine will run kind of "funky".
Take the car to a dealer with the new pcm still in the box. The dealer will have to have another mustang gt on the lot with a manual transmission in it. Call the dealer first and verify that and set up an appointment with them. Some dealers may tell you that they won't mess with it. Here's the instructions:
Bring both of your car keys with you. Have tech. pull the program out of another mustang gt with manual transmission in it. He will use his WDS Ford computer to do this. Make sure you reset your old pcm to stock program if you have a custom tune in it. You must have the factory program back in the old pcm before you remove the pcm. Install the new pcm and have tech. install the program that he took from the other car into your new pcm. He will then have to take both of your keys (not 1 key), but both and program them so the pcm will recognize them. He will then do a quick scan on your system for an "all clear", and you're done. If you have a custom tune for your mods, go ahead and install it in your new pcm and be on your way!
Section G
(Might be Omitted)
This picture shows a harness plug that is under your dash found just below your speedometer and tachometer. The male plug is just a dummy plug that connects the 2 red/light blue wires together. If you go ahead and put the 2 switches on the clutch pedal assy., you'll want to run the 2 wires that are red/lightblue to the bottom switch on the pedal assy. (starter enabler switch) The other 2 wires go to the top switch on the pedal assy. One white wire and one black wire. (cruise control deactivater switch).
Section H
Installation Photos